聯(lián)合預粉磨系統(tǒng)磨內結構的改造與效果
日期:2015-06-08 | 來源:新世紀水泥導報
本文2號水泥磨由C L F 1 7 0 / 1 0 0 輥壓機+ V X 3 0 0 0 V 型選粉機+ Φ 3 . 8 m × 1 1 m 水泥磨+IV3000-Sepa選粉機組成聯(lián)合預粉磨系統(tǒng),經(jīng)制造廠多次來公司調試,生產P•O42.5水泥臺時產量只..
本文2號水泥磨由C L F 1 7 0 / 1 0 0 輥壓機+ V X 3 0 0 0 V 型選粉機+ Φ 3 . 8 m × 1 1 m 水泥磨+IV3000-Sepa選粉機組成聯(lián)合預粉磨系統(tǒng),經(jīng)制造廠多次來公司調試,生產P•O42.5水泥臺時產量只有99.21 t/h,電耗達44.96 kW•h/t。本公司將系統(tǒng)中磨機內部結構進行改造,系統(tǒng)產量達到132.41 t/h,產量提高33.46%,電耗32.81 kW•h/t,電耗下降27%。本文就改造內容和效果進行介紹。
1 采用高細高產磨篩分技術隔板倉
隔板倉和篩分裝置的作用是控制各倉物料流速和防止串倉,以便控制調節(jié)前后倉能力平衡,控制磨內球料比在合理狀態(tài)。篩分裝置的篩網(wǎng)孔一般在1 mm~2.5 mm,便于使用小直徑研磨體來提高粉磨效率,其作用機理類似于選粉機。這種小篦縫大流速機械方式的磨內分級,使大顆粒返回前倉,使之進入后倉的物料粒度均齊,有利于提高細磨階段的粉磨效率。高細高產磨篩分技術生產水泥顆粒級配組成合理,與普通開流及閉路系統(tǒng)相比,同等細度(篩余時)比表面積更高。采用篩分隔倉板后磨內結構改造具體見表1。
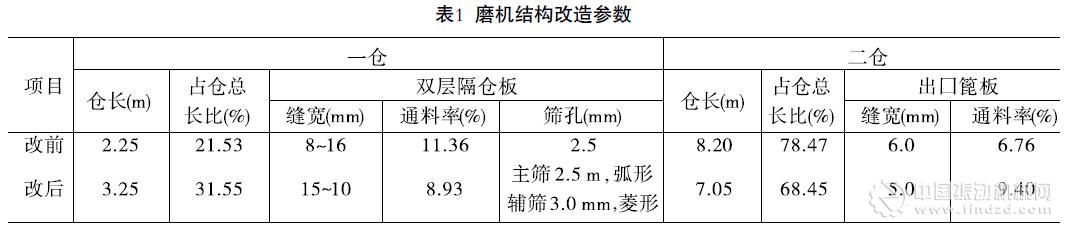
2 改變磨機倉位
輥壓機帶V選組成聯(lián)合粉磨工藝,入磨物料一般<2.0 mm,磨機主要是細磨和超細磨,但對物料仍有細碎任務,所以磨機細碎倉要短些,細磨倉要長些,這是粉磨的一般規(guī)律。筆者在生產實踐中得知,同規(guī)格磨機,生產同一品種,一倉長,出磨水泥細度偏大些,但比表面積比相同細度要高些,而且出磨水泥強度也相應提高。據(jù)我公司統(tǒng)計成品R0.045篩余為5.88%~5.10%,而比表面積只有280~300 m2/kg,這是細度與表比面積嚴重相背離。
成品R0.045篩余為8.10%時,比表面積352 m2/kg,這兩者相應較合適,只有成品細度值變大后,方可把比表面積提出來。筆者還認為成品細度小,而比表面積低,兩者背離較大,同時系統(tǒng)物料易磨性較差時,應采取增大一倉能力措施,以提高成品比表面積。
國內工藝系統(tǒng)磨機一倉長度為25%~36.54%范圍,而涇陽2號水泥磨一倉長度為21.53%,實際一倉偏短,可大膽延長一倉長度到31%左右,即一倉長度為3.25 m,割掉1.25處活環(huán),一倉從2.25 m改為3.25 m,二倉從8.20 m縮到7.05 m,從磨機整體看一倉適當延長0.25 m~0.75 m,后段倉相應縮短不一定影響后倉的細度能力,從磨內取樣,細磨倉總有一段篩余下降緩慢。改造后磨機倉長見表1。
實踐證明,一倉長度越接近磨機筒體直徑時,磨內鋼球運動規(guī)律越順暢,這樣有利于鋼球對物料沖擊而產生細微粉和顆粒裂紋,為后倉細磨創(chuàng)造條件。
3 改變研磨體級配
改造前后研磨體級配見表2。
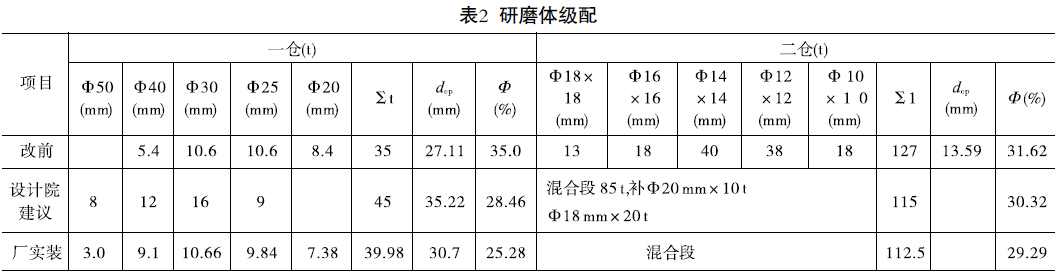
該系統(tǒng)入磨物料很細,R0.08篩在18%~30%范圍,可大大降低研磨體尺寸,為提高粉磨效果創(chuàng)造基本條件。另外,也有人認為破碎分離是提高粉磨效率的有效途徑,同時提出物料大于2.5 mm破碎效果好,物料小于2.5 mm是細磨效果好,所以該工藝系統(tǒng)對磨機粉碎只強調細磨和超細磨,對細碎有所忽視。筆者對系統(tǒng)入磨物料取樣篩析發(fā)現(xiàn),輥壓機系統(tǒng)狀態(tài)好時,入磨物料<1.0 mm,但也在物料中帶少量大于1.6 mm的顆粒,有時有大于2.36 mm的顆粒,所以,為保一倉能力,該系統(tǒng)用Φ40 mm鋼球是必要的,若系統(tǒng)物料易磨性差,入磨物料細度小、比表面積低,用少許Φ50 mm鋼球也是可行的。一倉采用Φ50 mm鋼球進行五級配,平均球徑從27.11 mm提到30.7 mm,填充系數(shù)從35%降到25.8%。從磨機標定知一倉球料比為7.5,偏低,所以一倉填充系數(shù)應控制在27%為宜。所以,一倉研磨體種類選擇與級配原則是確保一倉具有沖擊動能,對物料有沖擊粉碎作用,從而鋼球將物料在無序沖擊粉碎過程中產生小顆粒、微粉及顆粒裂紋,為后倉細磨創(chuàng)造條件,對小顆粒磨得更細,裂紋被解體后繼續(xù)進行粉磨,微粉對提高成品比表面積特別有利。
另外,水泥產品中的顆粒組成和顆粒形貌對水泥強度影響較大,利用一倉研磨體的動能沖擊,對改善上述參數(shù)創(chuàng)造條件,有利改善水泥產品顆粒的圓形度,從而提高水泥強度。
4 技改效果評價
4.1 改造前后產質量對比
改造前后產質量對比情況見表3、表4。
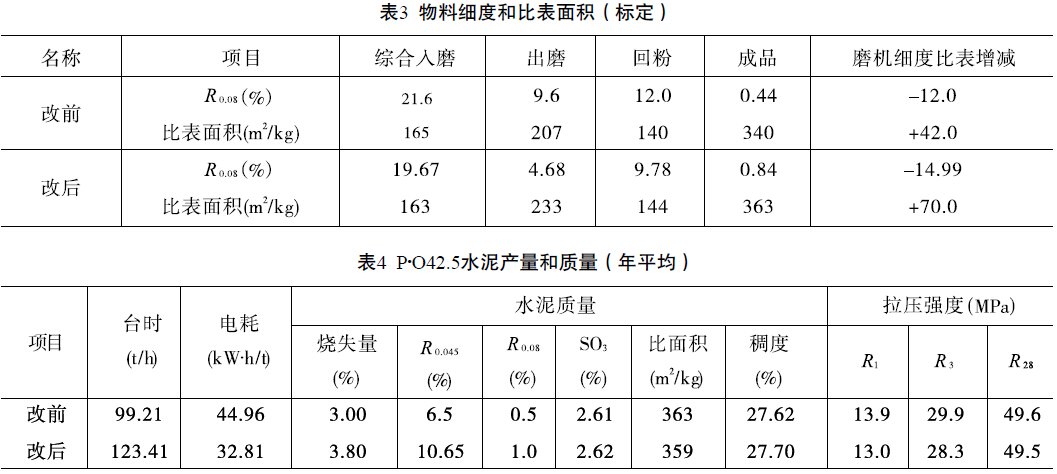
技改采取上述幾項措施,可能會出現(xiàn)一點過粉磨現(xiàn)象,這對提高成品比表面積是一種補償,對公司2號水泥磨的改造是有效的,對比改造前后物料篩余和比表面(表3),磨機出磨物料新增比表面積從42 m2/kg提到70 m2/kg,提高了28 m2/kg,提高了比表面積為磨機提產創(chuàng)造了條件,出磨細度從9.6%降到4.68%,降低了4.92%,成品比表面積從340 m2/kg提到363 m2/kg,提高了3.0 m2/kg。說明磨機粉磨效率有較大提高。改造前后生產P•O42.5水泥的產質量對比表見表4。從表4知,系統(tǒng)臺時產量從年均99.21 t提到年均132.41 t,提高了33.46%,電耗從44.96 kW•h/t降到32.81 kW•h/t,下降27.02%。
從表4知,改造前后出磨水泥年均比表面積為363 m2/kg和359 m2/kg,僅差4 m2/kg,差值僅為1.1%。而R0.045和R0.08篩余分別為6.5%和10.65%,與0.5%和1.0%相比,差值為38.97%與50%。從上述數(shù)據(jù)也驗證了延長一倉長度和提高一倉球徑,能提高一倉能力和研磨體沖擊動能,在相同比表面積下,R0.045、R0.08篩余值增大。充分說明上述措施的針對性和有效性。
公司對輥壓機循環(huán)系統(tǒng)進行標定,輥壓機的物料功耗為2.3 kW•h/t。一般來講,輥壓機物料功耗在2.0~5.0 kW•h/t的范圍內。公司輥壓機的物料功耗處于正常功耗范圍偏低一側。筆者認為公司輥壓機破碎作用大,物料粒徑大大降低,篩余下降,但物料晶格結構破壞產生微裂紋效果較差,微粉量少,物料比表面積偏低。從表3知入磨物料R0.08篩余為19.67%~21.60%,比表面積僅為163~165 m2/kg。
低于應達到的180~200 m2/kg范圍。對這種物料,磨機一倉要承擔對物料的細碎任務,就要提高一倉的沖擊動能,只有采取加長一倉長度和增大一倉鋼體球徑,來提高系統(tǒng)的粉磨效率,以提高系統(tǒng)產量和降低電耗。若入磨物料R0.08篩余在20%~30%,比表面積大于180 m2/kg~200 m 2/kg,磨機一倉細碎的功能很少,主要起研碎作用,就應控制一倉長度,適當?shù)亟档脱心ンw直徑等措施。
4.2 改造前后出磨水泥標準稠度需水量的變化說明
眾所周知,水泥標準稠度需水量與熟料礦物組成,尤其是C3A的含量與標準稠度需水量成線性關系,與熟料中堿含量、游離氧化鈣、黃心料、硫堿比,及窯內煅燒時還原氣氛和熟料冷卻速度及溫度等密切相關。這是水泥質量的基礎。出磨水泥標準稠度需水量還與出磨水泥溫度、石膏種類、混合材料品種與摻量、水泥細度、比表面積、粉磨工藝、水泥顆粒級配與形貌等有關。
我公司2 0 1 1 年初熟料標準稠度需水量由23.84%上升到26.33%;生產P•O 42.5水泥混合材摻量1 7 % ~ 2 0 % , 出磨水泥標準稠度需水量在28%~30%之間,而且這些水泥性能不夠穩(wěn)定。為了更好地滿足用戶需要,確保市場的競爭力,2011年5月生產P•O 42.5水泥,混合材摻量減到10%(詳見表5)。5~7月混合材停用粉煤灰,出磨水泥標準稠度從2011年1~4月的28.68%降到2011年5~7月的27.60%,8月混合材以礦渣代替煤礦石,出磨水泥標準稠度為25.90%。所以,改變混合材摻量和改變混合材品種是水泥制備環(huán)節(jié)降低水泥標準稠度的有效措施。
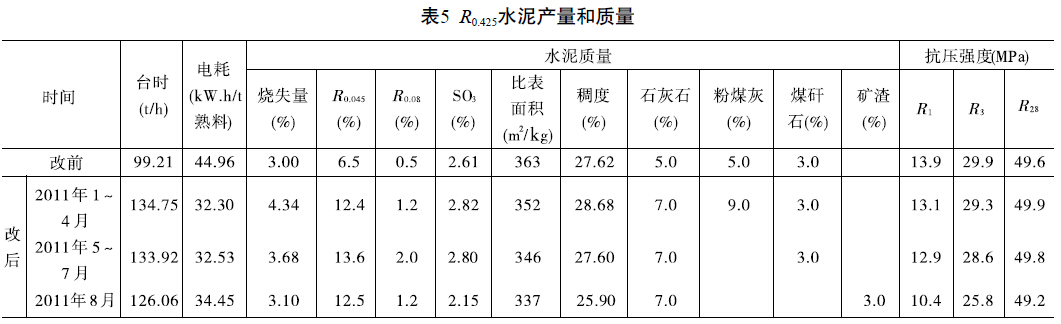
從表5知,雖然混合材摻量和品種的改變,使物料易磨性變差,磨機產量仍維持較好的水平,但出磨水泥篩余相應增加,比表面積相應有所下降,出磨水泥抗壓強度仍然保持相近,這也證明了技改的適應性和有效性。
責任編輯:劉麗娟
本文關鍵詞:粉磨系統(tǒng)
關于“粉磨系統(tǒng) ”的資訊
- 疫情影響,這條日產10000噸生產線投產可能推遲!(2020-03-27)
- 隴南公司生料粉磨系統(tǒng)項目通過驗收(2019-06-20)
- 江西中煙“基于晃動篩分與二級篩分裝置”發(fā)明專利獲公開...(2018-10-24)
- 影響圓振動篩設備篩分效果的三大要素(2018-10-22)
- 方大九鋼檢測部改造焦炭分層振動篩 更換不銹鋼篩板,增加耐腐蝕性...(2018-09-21)
- 年產能將達1000萬噸,朝陽區(qū)基本形成“臨時設施+固定設施”建筑垃圾資源...(2018-09-21)
- 威猛股份:起家于振動,壯大于篩分,未來,將成就于循環(huán)經(jīng)濟...(2018-08-31)